Safety isn’t just a checklist; it is a mindset that defines how we work, look out for one another, and deliver results, even in the most demanding environments. This was clearly demonstrated during our recent offshore project aboard TotalEnergies’ AKPO FPSO.
From April 3rd to May 12th, 2025, our team took on the critical task of recertifying and installing 67 PSVs. The project, carried out in multiple phases, was as much a display of technical skill as our shared commitment to safety, preparation, and teamwork.
A Pressure Safety Valve (PSV) is a vital safety device in any system that handles pressurised fluids or gases. A PSV is designed to act as a safeguard when pressure within a system begins to exceed safe levels. If a vessel, pipeline, or process unit experiences a pressure spike beyond what it was designed to handle, the PSV steps in automatically. It opens to release the excess pressure, either into the atmosphere or to a designated containment system, and then closes once normal conditions are restored. This swift, automatic action helps prevent catastrophic failures such as equipment rupture, fires, explosions, or toxic releases.
Beyond its mechanical function, a PSV also carries legal and regulatory weight. In industries like oil and gas, power generation, chemical processing, and manufacturing, PSVs are not optional; they are required by international standards and safety codes. Their presence is a clear marker that an organisation is committed to operational safety, compliance, and risk management.
What makes the PSV especially valuable is that it operates independently. Unlike pressure controllers or relief systems that require monitoring or manual intervention, a PSV is self-activating. This reliability and immediacy are what make it so critical, particularly in emergency scenarios where every second counts. But for a PSV to do its job effectively, it must be kept in optimal working condition.
Over time, constant exposure to high pressure, temperature fluctuations, corrosive materials, and mechanical stress can degrade its components. Springs may weaken, seals may wear out, and seats may begin to leak. These issues might seem minor at first, but in a safety-critical device, even the smallest malfunction can lead to serious consequences.
That’s why recertification is not just recommended, it’s essential. Recertifying a PSV involves a thorough process designed to verify that the valve will perform accurately and reliably under pressure.
The process typically starts with a careful inspection and removal of the valve from service. It is then disassembled and cleaned, with each component inspected for wear, corrosion, or deformation. Any damaged parts are either repaired or replaced. The seating surfaces may be re-machined or lapped to ensure a proper seal. Once reassembled, the valve undergoes a series of tests to confirm that it opens at the designated set pressure and reseats correctly without leakage. The final step is certification: the valve is tagged, documented, and returned to service with full confidence that it will respond as designed in the event of overpressure.
Our Offshore Recertification Process
BOG’s valve engineers brought not just experience, but a full recertification protocol to the AKPO FPSO. The campaign included:
- Initial functional assessments of each PSV in-situ to determine suitability for removal.
- Controlled dismantling and tagging to ensure traceability.
- Testing using calibrated mobile test benches brought offshore by our team.
- Compliance with API 576 & API 527 guidelines for valve inspection and leakage limits.
- Reinstallation and leak-tight testing under live process conditions.
BOG’s Unique Advantage
Bell Oil & Gas is proud to be one of the few indigenous Nigerian companies with in-house PSV recertification capability, supported by:
- An API-compliant valve workshop
- Certified valve technicians with offshore experience
- A fully integrated preservation, traceability, and certification process
- Field-ready tools and documentation aligned with major IOC requirements
Our approach saves clients from the cost and delay of shipping valves abroad for recertification, making us a strategic local partner for critical valve integrity management. BOG’s Valve Assembly, Maintenance Plant in Nigeria, played a key role in preparing the recertification kits, test equipment, and documentation processes in advance. This made the offshore campaign both efficient and compliant.
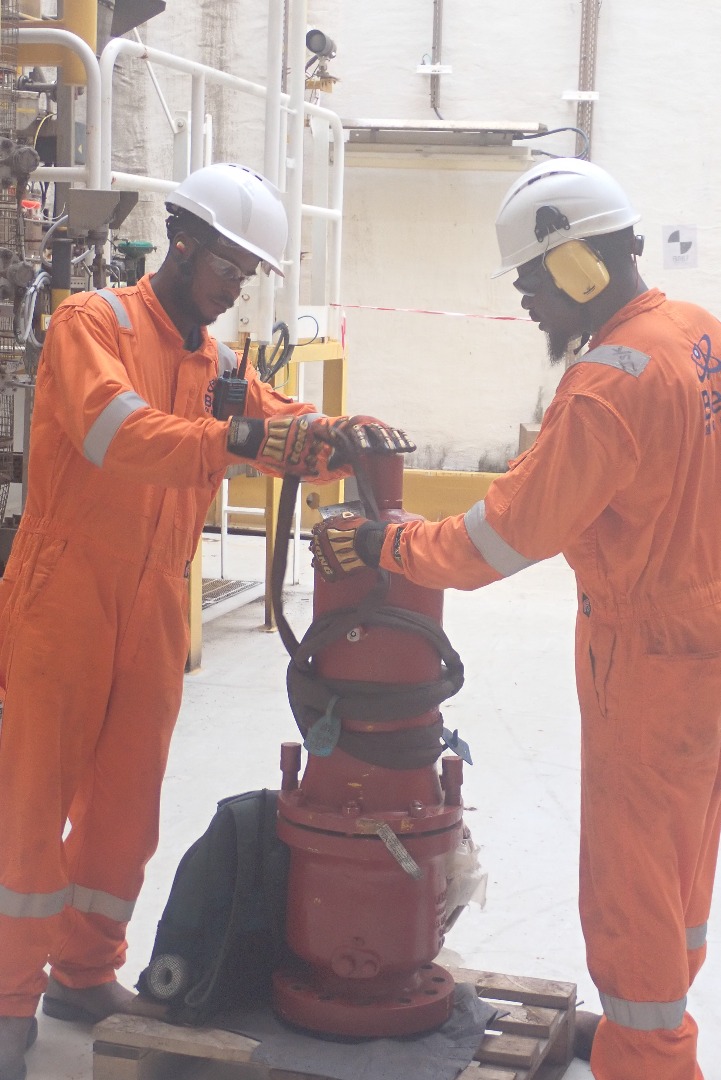
Equally crucial was the pre-mobilisation medical fitness check. Offshore work is demanding, and the well-being of every team member is paramount. Comprehensive health assessments ensured that all personnel were physically prepared to meet the challenges of the offshore environment.
Once onboard the AKPO FPSO, the team’s dedication to safety shone through in every task. Beyond recertifying PSVs, the team engaged in hazard identification, toolbox talks, and permit-to-work systems. The result? A successful campaign completed without any lost-time injuries (LTIs), a testament to the collective vigilance and professionalism of our team.
BOG’s achievements on the AKPO FPSO are not just about numbers, they’re about people. People who train, prepare, and execute with excellence. People who understand that offshore work demands the highest standards of safety and teamwork. Our team’s success reflects the values we uphold at BOG: safety, integrity, and a commitment to excellence in all we do.
We remain proud of our team and committed to raising the bar for safe, high-quality offshore operations.
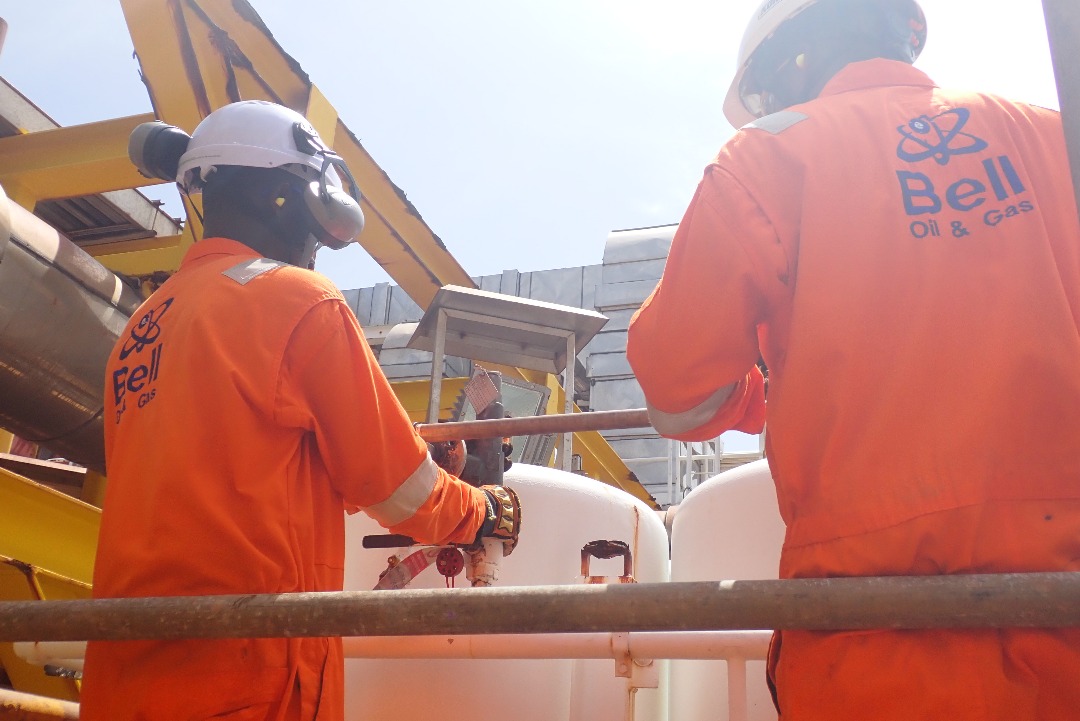
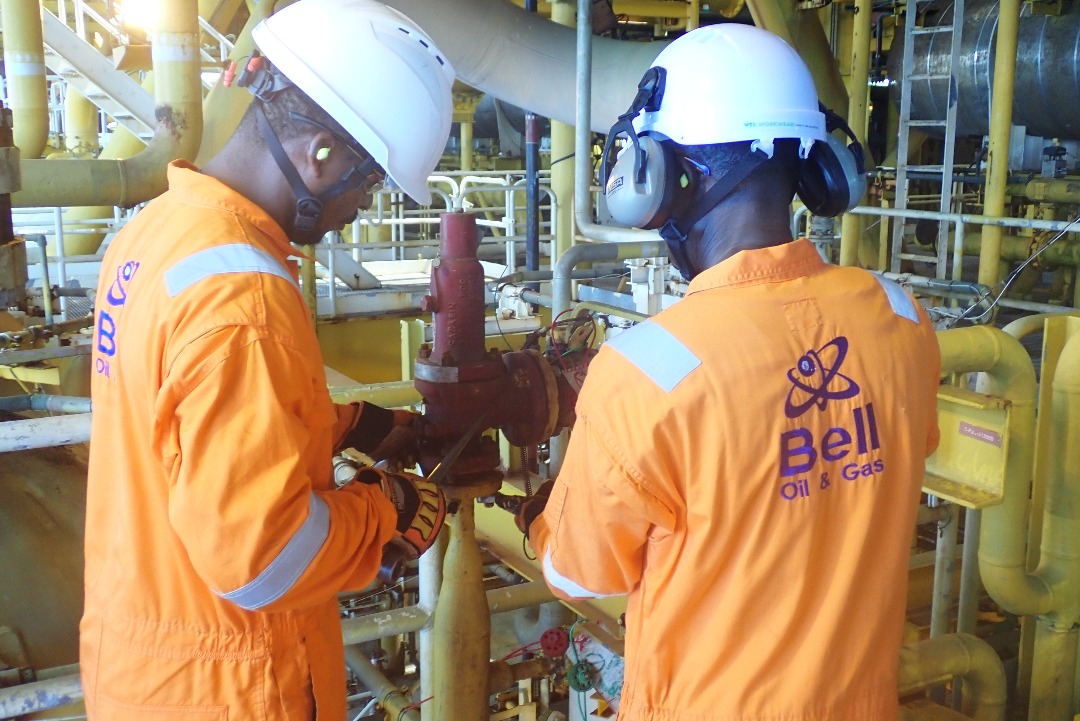